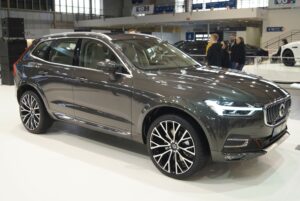
By 2021, Volvo’s new Charleston plant will have a capacity of 150,000 for production of the XC90.
The 2017 American Automotive Summit was held on November 28-29 at The Henry, Autograph Collection in Dearborn, MI. It was an extremely successful event and we were proud to have top industry influencers share their thought leadership, including representatives from OEM’s Volvo, Toyota, Ford, and Kia. Here’s what we learned.
Katarina Fjording, VP, Purchasing and Manufacturing, Americas at Volvo Car US Operations, told the audience about how Volvo is bringing jobs back to the United States with a new plant in Charleston, South Carolina. They have made this decision for many reasons: to secure a global operational presence, build where they sell and sell where they build, and send a strong message to their dealers and consumers that they are serious about the North American market. Starting in 2018, they will produce 65,000 all-new Volvo 560s in this plant, and by 2021 will have a capacity of 150,000 for production of the XC90. They will add 2000 jobs in the short term, and 4000 long term. But this mega greenfield project brings with it many challenges, which Fjording expanded on to a captive audience. Within this one major project, there are about 8 other sizable projects: the launch of a brand new vehicle, the construction project, the installation project, the logistics footprint, local & regional sourcing, production setup, a major IT project, and establishing an industrial operations organization.
Jamie Bonini, VP, Toyota Production System Support Center at Toyota shared case studies on how the Toyota Production System (TPS) is helping industry and non-profits alike become lean and improve customer service. He defines TPS as “an organizational culture, created and sustained by a philosophy, that underlies some technical tools, that must be supported by a managerial role to develop people to solve problems to drive improvement.” He demonstrated how TPS has improved lead time and profitability in a job shop making stainless steel components, how they have made the New York State government more efficient, and decreased wait times for eye surgeries among patients who previously could have gone blind waiting for a surgery.
Stuart Countess, CAO & VP, Kia Motors Manufacturing Georgia followed Bonini and credited the TPS system as the foundation of a lot of what they have done at Kia to improve quality. He spoke on how Kia took the #1 spot in Quality in the JD Power survey two years in a row, shedding a low-quality reputation. 40% of the cars included in this survey came from the West Point, Georgia plant, which started production in 2009 with a workforce that had never built cars before. Countess talked about how the company blends American and Korean culture, how they developed the Kia Way, and how they plan to keep the top spot in quality.
In another transformation story, Bennie Fowler, GVP, Quality and New Model Launch at Ford Motor Company, shared how Ford went from a record $12.7 billion loss in 2006 to the success they are today. He called it “the largest lean/sigma project ever imagined,” and said its value up to this point is about $70 billion. This required a fundamental overhaul of their quality strategy.
To view the full presentations of all these speakers and more, request access to our knowledge center.
Join us next year at the American Automotive Summit! usautosummit.com