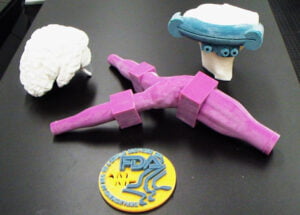
3D printed models of a brain, blood vessel, surgical guide and an FDA medallion, printed on FDA 3D printers.
One of the promises of additive manufacturing is the ability to go after niche markets with low volume production of unique parts. What application could be more apt for this technology than the human body?
Last month, the FDA issued a statement providing guidance to manufacturers on technical aspects of additive manufacturing, clarifying what the FDA recommends manufacturers include on submissions for 3D printed medical devices. The FDA has, so far, approved over 100 3D printed medical devices, including knee replacements, custom skull/facial reconstructions, and even a 3D printed drug, called Spritam, which is used to treat seizures. The FDA has categorized this technical guidance as a “leap-frog” guidance, explaining that it is just a mechanism to share initial thoughts in order to bridge where we are today with the innovations of tomorrow.
3D printing is currently being used extensively for surgical planning, allowing physicians to see a realistic 3D model of the specific body part they will be operating on, be it a hip or a heart. This allows for a more efficient surgery, fewer surprises in the operating room, and better patient outcomes. According to a recent study by University of California San Diego and Rady Children’s Hospital, using 3D printing for surgical planning results in an average of $2700 savings per surgery, due to the high cost per minute of operating room time.
Just as 3D printing in the automotive and aerospace sectors are moving beyond simply protoyping applications, 3D printing in the medical device field is moving beyond planning purposes.
Some exciting innovations include the application of 3D printing to:
- Create medical equipment quickly and in a cost-effective way
- Create personalized prosthetics and implants, including synthetic organs
- Print biomaterials, such as blood vessels and bones
Johnson & Johnson’s 3D Printing Center of Excellence is working to change the landscape of healthcare through 3D printing innovations. Some of their projects include custom knee implants and instruments developed based on a CT or MRI scan of a patient’s anatomy. “Through 3D printing technology, we can print exactly what the patient needs to replace the degraded bone. The implant can be made based on a CT or MRI scan from thousands of miles away,” says Joe Sendra of Johnson & Johnson.
We are thrilled to have Sam Onokuri, Head of Johnson & Johnson’s 3D Printing Center of Excellence as a speaker at Generis’ American Biomanufacturing Summit where he will give an innovation spotlight on “Looking toward a Future of Personalized Healthcare through 3D Printing”.
Join the conversation on innovative manufacturing technologies at our upcoming events!
- American Manufacturing Summit | Lombard, IL | March 27-28
- American Biomanufacturing Summit | San Francisco, CA | June 14-15
- American Medical Device Summit | Lombard, IL | October 24-25
Comments
3D printing has been around for awhile now, but it’s great to see it expand to actual use cases. So many medical devices are designed to meet the needs of one person, so the adaptability of 3D printing is a real pro.