The environment facing automotive-related manufacturers is fierce. Changing regulations, competitor landscape, technology and customer preferences, along with a fluid global economy, create challenging conditions for automakers and their suppliers.
The Austin Company understands this landscape.
This is an excerpt from an interview Generis Group did with Brandon Davis, Vice President of Operations and General Manager at The Austin Company prior to the American Automotive Summit 2018.
“How can automotive manufacturing facilities decrease project capital costs through engineering and re-design concepts?
There are a few ways to look at reducing costs today, compared to how traditional automotive plants used to be designed and built. Throughout most of my career in the industry, we would build plants with what I would call ‘oversized’ structural steel. By doing this, we built in maximum flexibility for the plant, so equipment could easily move around and the plant could be easily adapted in the future, as much of the production processes were “hung loads” from the structure. As the industry has evolved, equipment has become lighter, many production processes can now be floor-mounted, and – in general – equipment has become more flexible and able to support different product types. In this setting, we are working hard in the production layout efforts to see what really needs to be supported from the structure and to design structures specifically for what is needed. That reduces the cost of the facility construction and saves the use of our natural resources.
As it relates to flexibility for future production changes or modification, we have not seen significant issues that couldn’t be addressed with the proper engineering. There are also, of course, sustainable approaches that drive decreased capital costs. We can collect gray water for reuse. We can capture process heat for reuse or cogen. When you’re making things, automotive or otherwise, you have a lot of energy from parts, machines and the manufacturing process in general. You can use that heat or steam to generate power. We’ve done that just recently, where we have taken process heat and piped it to a different part of the facility, rather than having heating units. This all goes along with Lean Design and Construction practices, which we have adopted through following the lead of manufacturers like the automakers and their suppliers.”
Questions discussed:
- How can automotive manufacturing facilities decrease project capital costs through engineering and re-design concepts?
- What are some key strategies to optimize operational costs through plant layout planning?
- How can automotive manufacturers reduce errors, improve quality and save money with a fully integrated BIM environment?
- What are the necessary steps to leading a successful plant expansion for OEMs and suppliers to achieve their target production date?
- How can automotive manufacturers drive rapid project delivery? What steps has The Austin Company taken to help their clients achieve this delivery, and what has the outcome been?
Click through to access the full interview here.
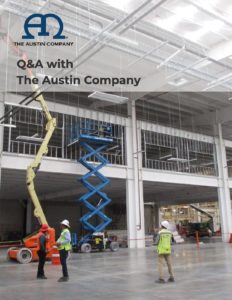